TPT offers various technologies for prototyping and short run production of castings.
Rapid Vacuum Investment Casting
Rapid vacuum investment casting is a combination of Rapid prototyping and Vacuum casting technologies. Master patterns are made using rapid prototyping techniques followed by investment casting process.
Steps involved in Rapid Vacuum Investment Castings
3D CAD model is the Input for our process .This needs to be provided by the customer in STL, IGES or STEP format. |
Step 1: | Producing Rapid Prototype Master using SLA or CNC machining. |
Step 2: | Preparation of Silicon Rubber Mould (SRM) using the RP Master pattern in Vacuum |
Step 3: | Produce wax pattern (replica of the master pattern) in the SRM. |
Step 4: | Construction of wax pattern tree by adding sprue, runners and gates. The wax tree is placed in a casting flask |
Step 5: | Mixing of ceramic investment slurry and pouring under vacuum in to the casting flask . Now the wax tree is completely encapsulated in the investment slurry . |
Step 6: | The flask is placed in furnace for drying of ceramic and melt out of wax. |
Step 7: | The flask with the ceramic cavity is placed in the casting machine. |
Step 8: | Required amount of metal alloy is melted in the induction furnace. Pouring is done under vacuum and over pressure. |
Step 9: | Flask is removed . The ceramic mould is broken. The metal tree will be fettled and cleaned to get the final castings |
Step 10: | Heat treatment |
Step 11: | Machining |
|
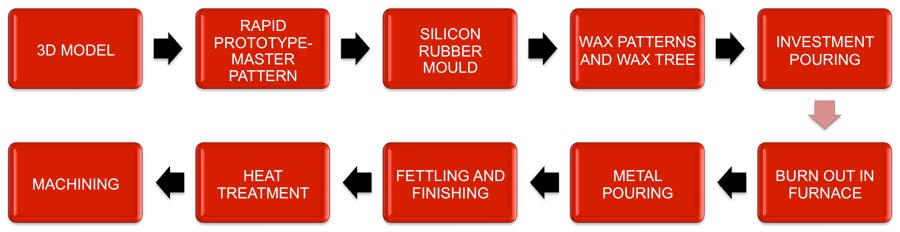 |
|
Typical Alloys Casted: LM25/A356, A357, LM4, ZAMAK |
Contact Us for detailed information on our process. |
Advantages
- Vacuum reduces porosity & inclusion
- Cost effective
- Precise dimensional control
- Superior surface finish
- Intricate shapes can be cast
- Variety of aluminium and zinc alloys can be cast
- Reduce Material wastage
- Reduce machining required
Traditional Investment Casting
Steps involved in Traditional Investment Castings
Step 1: | Cad data and 2D drawing from Customer |
Step 2: | Aluminum Die Making for Wax Patterns |
Step 3: | Wax Pattern Production from Injection Press |
Step 4: | Construction of wax pattern tree by adding sprue, runners and gate |
Step 5: | Ceramic Shelling process to form ceramic shell over wax patterns |
Step 6: | De waxing in Autoclave and ceramic shell burn out |
Step 7: | Metal Pouring under Vacuum or Open Pouring |
Step 8: | Ceramic shell breaking , fettling and finishing |
Step 9: | Heat treatment and sand blasting |
Advantages
- Ideal for Small Batch Production
- Good for precise components
- Good Dimensional Stability
- Die Cost is less compared to PDC
- Variety of Alloys can be cast
Quick Cast and Cast Form Techniques Casting
Steps involved in Quick Cast and Cast Form Techniques Casting
Step 1: | Cad data and 2D drawing from Customer |
Step 2: | Plastic Patterns from SLA or SLS additive layer techniques |
Step 3: | Construction of tree with plastic pattern and wax gating system |
Step 4: | Ceramic Shelling process to form ceramic shell over plastic patterns |
Step 5: | De waxing and ceramic shell burn out |
Step 6: | Metal Pouring under Vacuum or Open Pouring |
Step 7: | Ceramic shell breaking , fettling and finishing |
Step 8: | Heat treatment and sand blasting |
Advantages
- Ideal for 1-3 nos casting
- Good for design Validation
- Short Lead times
- Any Intricate Shape Can be cast
Ceramic Mould Casting
Steps involved in Ceramic Mould Casting
Step 1: | Cad data and 2D drawing from Customer |
Step 2: | Plastic Patterns from FDM or CNC machining |
Step 3: | Mould Making using ceramic |
Step 4: | Mould Baking |
Step 5: | Metal Pouring |
Step 6: | Ceramic shell breaking , fettling and finishing |
Step 7: | Heat treatment and sand blasting |
Advantages
- Ideal for simple castings
- Comparable to Sand Casting
- Quick Turn around time
- Surface finish better than sand casting